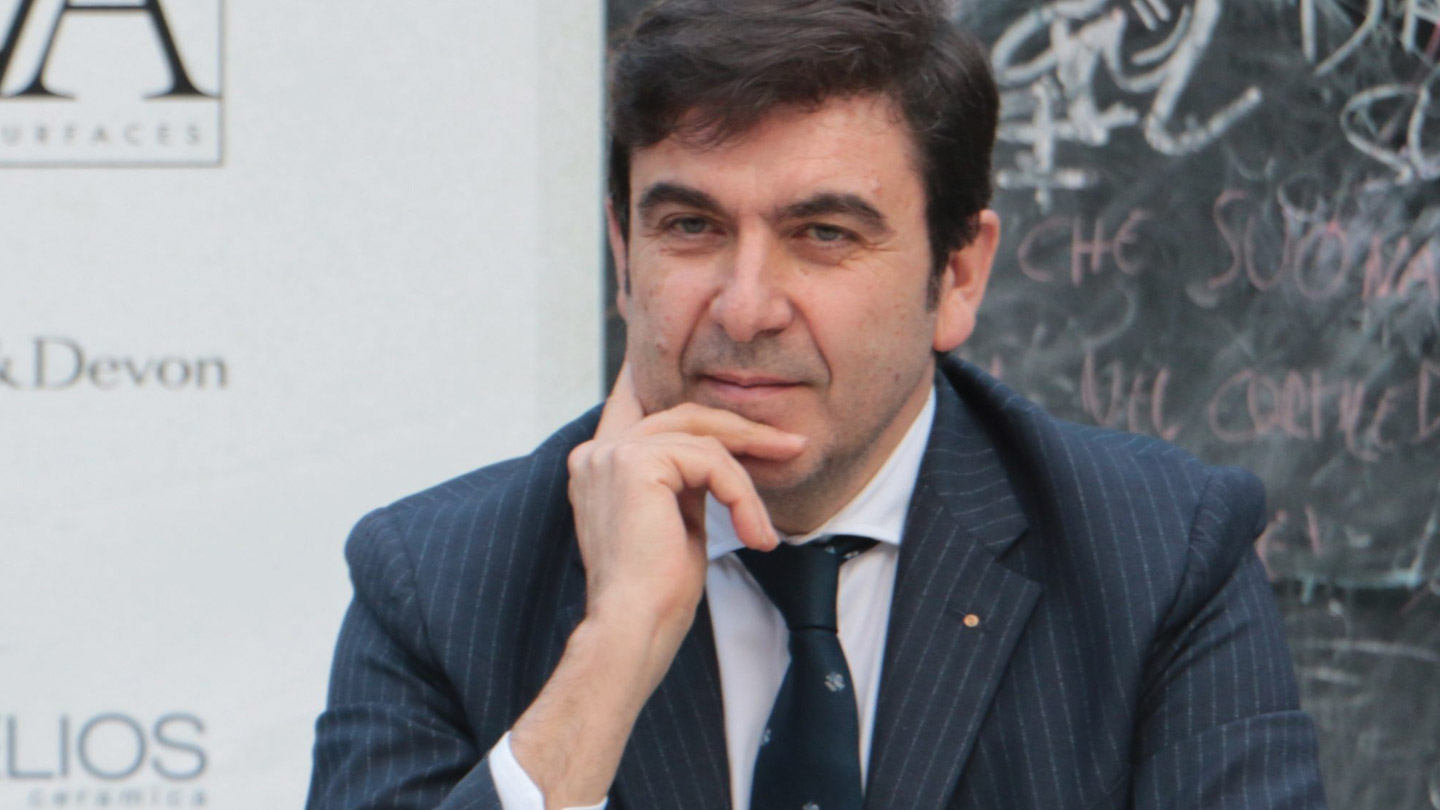
Clean ceramic between filters and magnets
In travel to the Italcer of Sassuolo, tip of an iceberg of the investments in a district that in 15 years has reduced by half the index of the Sassuolo accidents.
The truck leaves Via Emilia and goes straight into the courtyard. It pours its sand compounds and processing waste directly onto a conveyor belt that slides along two parallel rows of silos. On the conveyor belt, a long “separator” bar – affectionately called “knife” – deals with the precise deviation of each mixture in its reference silos. It happens every 3 hours, from Monday to Friday. There are no hands. It’s all automated and previously planned in order to work.
The “life” of a tile 4.0 begins in a factory in the ceramic district of Sassuolo. We are at the Italcer plant in Rubiera where, as in all ceramics, we work on 3 shifts of 8 hours. With 26 employees per shift are produced 18.000 square metres of ceramic per day.
The Sassuolo district has never stopped innovating. And thanks to the intersection with industry 4.0, the digitization of lines, predictive analysis of the “health status” of machinery, the increasingly sophisticated systems of odour and noise filtration, has greatly improved in a few years the quality of the environments in the production plants and especially the safety at work.
Only in 2018 – data by Confindustria Ceramica – investments amounted to EUR 508.2 million, almost 10% of the turnover of the sector. A value that allowed the whole industry to exceed 2 billion in the five years. A huge effort, favored by the tax incentives of Industry 4.0 for the modernization of the plants, which the tile industry has been able to capture more than other Italian industrial sectors, aiming at a recovery of competitiveness through more advanced technologies.
And in fact from the quality control station it is possible to observe – almost as in a video game – the supplying process and to carry out random checks on both the quality of the materials and their resistance.